A Comprehensive Overview to the Process and Advantages of Plastic Extrusion
In the large realm of manufacturing, plastic extrusion emerges as a essential and extremely reliable procedure. Altering raw plastic right into constant accounts, it provides to a wide variety of sectors with its exceptional adaptability.
Comprehending the Basics of Plastic Extrusion
While it might appear complex at very first glimpse, the procedure of plastic extrusion is fundamentally straightforward. The procedure starts with the feeding of plastic material, in the kind of granules, powders, or pellets, into a heated barrel. The designed plastic is after that cooled, strengthened, and reduced into desired lengths, completing the process.
The Technical Refine of Plastic Extrusion Explained
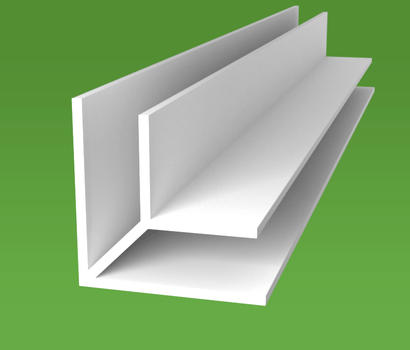
Sorts Of Plastic Suitable for Extrusion
The option of the ideal kind of plastic is a crucial facet of the extrusion procedure. Various plastics provide one-of-a-kind buildings, making them much more fit to certain applications. Recognizing these plastic types can dramatically enhance the extrusion process.
Comparing Plastic Extrusion to Various Other Plastic Forming Methods
Recognizing the kinds of plastic ideal for extrusion leads the way for a wider discussion on just how plastic extrusion stacks up against other plastic creating approaches. Plastic extrusion is unmatched when it comes to creating constant accounts, such as seals, pipes, and gaskets. It also permits for a regular cross-section along the length of the item.
Key Advantages of Plastic Extrusion in Production
In the realm of production, plastic extrusion provides many significant benefits. One significant benefit is the cost-effectiveness of the process, that makes it a financially appealing manufacturing technique. Furthermore, this strategy offers remarkable item adaptability and improved manufacturing rate, therefore raising general production efficiency.
Cost-Effective Manufacturing Technique
Plastic extrusion leaps to the forefront as an affordable manufacturing method in production. This procedure stands apart for its capacity to create high volumes of material quickly and effectively, giving suppliers with substantial financial savings. The key cost benefit is the capacity to use more economical resources. like this Extrusion makes use of polycarbonate products, which are less expensive contrasted to porcelains or metals. Further, the extrusion procedure itself is fairly straightforward, lowering labor prices. Furthermore, plastic extrusion calls for much less power than conventional production methods, adding to reduced functional costs. The procedure also reduces waste, as any type of defective or excess materials can be recycled and recycled, supplying another layer of article cost-effectiveness. In general, the economic benefits make plastic extrusion an extremely attractive choice in the production sector.

Superior Item Versatility
Past the cost-effectiveness of plastic extrusion, another significant benefit in manufacturing depend on its superior item adaptability. This process permits the development of a large selection of products with varying sizes, forms, and styles, from simple plastic sheets to detailed accounts. The versatility is credited to the extrusion pass away, which can be customized to produce the desired product design. This makes plastic extrusion an excellent option for industries that require personalized plastic elements, such as auto, construction, and product packaging. The ability to produce varied products is not just advantageous in conference particular market needs however additionally in enabling manufacturers to discover brand-new line of product with minimal capital expense. Basically, plastic extrusion's item adaptability cultivates advancement while improving operational effectiveness.
Boosted Production Rate
A considerable benefit of plastic extrusion exists in its enhanced manufacturing rate. Couple of other production processes can match the rate read this of plastic extrusion. Furthermore, the capacity to preserve constant high-speed manufacturing without compromising product top quality establishes plastic extrusion apart from other techniques.
Real-world Applications and Impacts of Plastic Extrusion
In the world of production, the strategy of plastic extrusion holds profound relevance. This procedure is widely made use of in the manufacturing of a range of products, such as plastic tubing, home window frameworks, and weather condition stripping. As a result, it substantially influences sectors like building, product packaging, and automotive industries. Its influence prolongs to daily items, from plastic bags to toothbrushes and disposable flatware. The financial advantage of plastic extrusion, largely its affordable and high-volume output, has actually reinvented production. The ecological effect of plastic waste remains a concern. The market is constantly striving for advancements in naturally degradable and recyclable materials, showing a future where the advantages of plastic extrusion can be maintained without jeopardizing environmental sustainability.
Final thought
In final thought, plastic extrusion is a reliable and extremely reliable technique of transforming resources into diverse items. It offers countless advantages over other plastic developing methods, including cost-effectiveness, high outcome, marginal waste, and style adaptability. Its effect is greatly felt in numerous sectors such as building and construction, vehicle, and consumer goods, making it a crucial procedure in today's manufacturing landscape.
Diving much deeper into the technological process of plastic extrusion, it begins with the option of the ideal plastic material. Once cooled down, the plastic is cut into the needed lengths or wound onto reels if the item is a plastic movie or sheet - plastic extrusion. Comparing Plastic Extrusion to Various Other Plastic Forming Methods
Comprehending the types of plastic appropriate for extrusion paves the method for a broader discussion on just how plastic extrusion stacks up against other plastic creating approaches. Couple of other production processes can match the rate of plastic extrusion.